Восстановление герметичности трубопроводов с применением металлополимерных материалов.
Ищенко А. А. , профессор, доктор технических наук, Приазовский государственный технический университет.
Применение металлополимерных материалов (МПМ) при проведении ремонтно-восстановительных работ в различных отраслях промышленности позволяет существенно сократить как стоимость таких работ, так и время их выполнения.
Широкое применение новых ремонтных технологий тормозится из-за естественного недоверия ремонтного персонала к МПМ, а также из-за отсутствия системных исследований свойств и способов применения материалов, доказывающих эффективность их использования.
В Приазовском государственном техническом университете были выполнены исследования адгезионной прочности МПМ и поиск оптимальных вариантов восстановления вышедших из строя участков трубопроводов.
В исследованиях применялся известный метод равномерного отрыва с применением статических разрушающих нагрузок. Испытания проводились на разрывной машине Р-20 с предельной силой растяжения 200 кН, скорость перемещения ползунов составляла 300 мм в минуту, допускаемая погрешность измерения +-1%. Форма образцов и схема нагружения МПа, применяемых в экспериментах, показана на рис. 1, а размер составлял 20 мм в узкой части и 25 мм в широкой части. Общая высота образца 45 мм. Образцы удерживались во время испытания специальными захватами с шарнирными устройствами, предотвращающими воздействие на образцы иных нагрузок, кроме растягивающих.
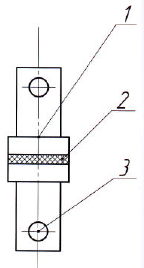
Рис. 1. Схема проведения испытания.
После зачистки контактных поверхностей образцов, их обезжиривания и просушивания на оба из них наносили путем втирания слой металлополимера, а затем образцы соединяли, при этом слой металлополимера составлял от 0,9 до 1,1 мм.
Эксперименты выполнялись с применением известного металлополимерного материала «мультиметалл» немецкой фирмы «Diamant-металлпластик GMBH». Результаты проведенных испытаний адгезионной прочности материалов «мультиметалл» при различных способах зачистки поверхности образцов позволяет дать оценку этому показателю.
Сравнение адгезионной прочности соединения образцов, контактная поверхность которых обрабатывалась в трех вариантах: иглофрезой, наждачным кругом и торцевой фрезой, в случае использования одного и того же материала «мультиметалл-сталь 1018» показало, что наилучшие результаты, которые характеризуются средней величиной 30 МПа, достигаются после обработки образцов шлифовальным кругом. В случае обработки поверхности иглофрезой и торцевой фрезой адгезионной прочность снижается на 20-25% по сравнению с зачисткой наждачным кругом.
Поскольку существует две модификации материала «мультиметалл»: пастообразный и жидкотекучий, то очень часто при использовании пастообразного не всегда качественно удается выполнить нанесение первого адгезионного слоя из-за невозможности как положено втереть этот слой в поверхность образца. Для улучшения его сцепления с металлом возможны два приема. Первый – наносить первый слой с подогревом материала до 40-45°С. Такой нагрев делает пастообразный «мультиметалл» более пластичным, что позволяет выполнить необходимые требования по втиранию первого слоя. Однако подогрев не всегда возможен или удобен в производственных условиях, поэтому применяют в качестве грунтовки при нанесении первого адгезионного слоя «мультиметалл» жидкотекучий. Результаты испытаний позволили установить, что применение «мультиметалла» жидкотекучего в качестве первого адгезионного слоя повышает адгезионную прочность соединения на 15-25%. Близкий к этому результат дает и использование предварительного подогрева «мультиметалла» пастообразного. Таким образом, в производственных условиях для повышения адгезионной прочности может быть использован один из названных приемов, в зависимости от наличия «мультиметалла» жидкотекучего или возможности подогрева «мультиметалла» пастообразного.
Если один путь проверки материалов на адгезионную прочность – это испытание загерметизированных с помощью МПМ сосудов под давлением. Для этого в сосуде заранее выполнялись отверстия различного диаметра. Затем поверхность сосуда вокруг отверстий подготавливалась к нанесению материала (т.е. очищалась, обезжиривалась), и наносился материал «мультиметалл». После 24 часов, отведенных на полимеризацию МПМ, проводились испытания на гидравлическом прессе, закачивая масло под давлением в сосуд до появления течи из-под латки или полного ее отрыва. Такие испытания позволили установить, что при размере отверстий диаметром до 5 мм подобные латки выдерживают давление до 30 МПа.
В подтверждение полученным результатам можно сослаться на опыт выполнения испытаний в системе Газпрома (Россия). Лентрансгазома в Гатчине, где производились натурные гидравлические испытания труб со сквозными дефектами, отремонтированных с помощью материала «мультиметалл». При этом испытаниям подвергались трубы диаметром 337 мм с толщиной стенки 9,0 мм. Различные по конфигурации дефекты на испытуемом участке трубы составили по площади от 315 мм2 до 480 мм2. Круглые сквозные отверстия герметизировались по технологии, изображенной на рис. 2. После нагружения до 15 МПа появилась течь. Испытания также предполагали чередования нагружения до 7 МПа с резким сбросом испытательного давления.
Еще один пример – это испытания, которые были проведены в Институте композиционных технологий им. Н. Э. Баумана (Москва). В этих испытаниях образцы труб с отверстиями диаметром 2 мм и зоной наложения материала диаметром 20 мм загерметизировали материалом «мультиметалл-сталь». Испытания включали в себя циклы нагружения, моделирующие реальные климатические условия северных и южных районов России, в комплексе с испытаниями на вибрационные нагрузки.
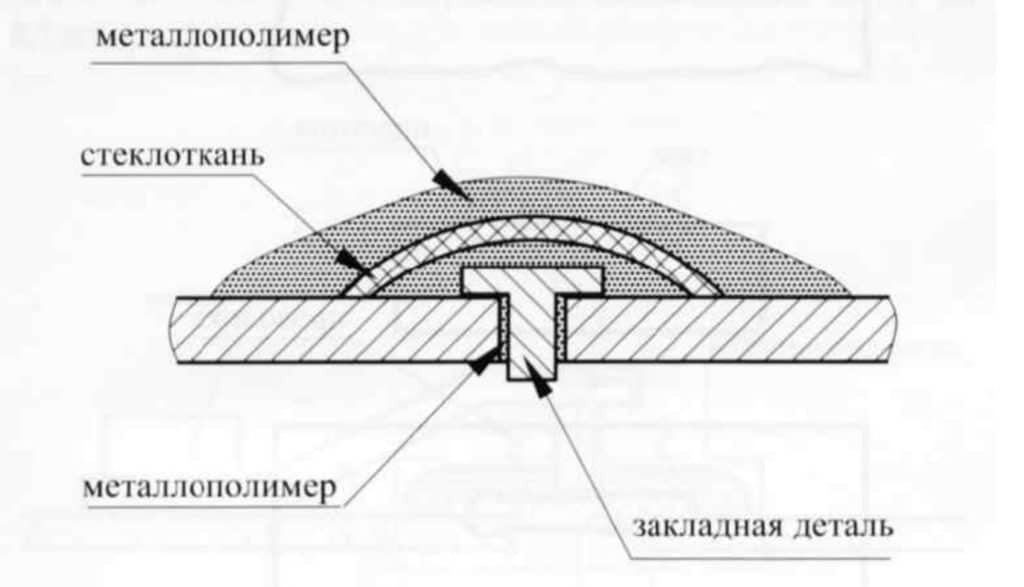
Рис. 2. Герметизация дефектного участка трубопровода с использованием закладной детали и стеклоткани.
После вибрационных и климатических испытаний образцы были испытаны под давлением, как в статическом, так и в циклическом режиме нагружения.
Например, 320 циклов нагружения давлением 40-75 МПа приравнивались к году эксплуатации объекта в реальных условиях. В испытаниях образцы выдерживали до 3200 циклов, что соответствует 10 годам эксплуатации. В целом, оценивая результаты лабораторных и натурных экспериментов, можно сделать вывод о том, что дефекты в виде трещин и небольших свищей с площадью до 100 мм2 могут быть без затруднения отремонтированы с помощью МПМ без использования закладных элементов. В этом случае образованная латка из «мультиметалла» удерживается лишь за счет сил сцепления МПМ с металлом. С другой стороны, при таком размере дефекта площадь соединения мультиметалла с металлом вокруг этого дефекта будет как минимум в 3 раза больше, а это означает, что, например, при давлении 10 МПа усилие, действующее на латку, составит около 785 Н, что в пересчете на требуемую адгезионную прочность составит всего 3,3 МПа. Таким образом, если не принимать во внимание упомянутые выше жесткие климатические условия и снижение в этих условиях адгезионной прочности при таком ремонте будет равен 8-10, учитывая, что этот показатель у «мультиметалла» достигает 30 МПа.
Вопросам адгезионной прочности МПМ было уделено особое внимание. В частности, на основании натурных испытаний сделаны очень важные для практического применения выводы. Например, длительный перерыв между операциями обезжиривания и нанесения материала может снизить адгезионную прочность почти в 2 раза. Поэтому предлагается не выходить за рамки двухчасового интервала между обезжириванием и нанесением полимерного материала.
В настоящее время разработана целая гамма различных устройств и приспособлений, позволяющих значительно повысить эффективность применения МПМ при ремонте трубопроводов. Например, усилить латку, выполненную с помощью МПМ, можно путем использования стеклоткани в качестве армирующей манжеты. Вначале адгезионный слой полимера втирается в поверхность трубы вокруг дефектного места, в том числе и по всей плоскости прилегания манжеты. Манжета с двух сторон промазывается МПМ перед ее укладкой, а после укладки сверху манжеты и сверху примыкающих боковых зон наносится окончательный слой, покрывающий в целом всю дефектную зону с примыкающими участками, как показано на рис. 3.
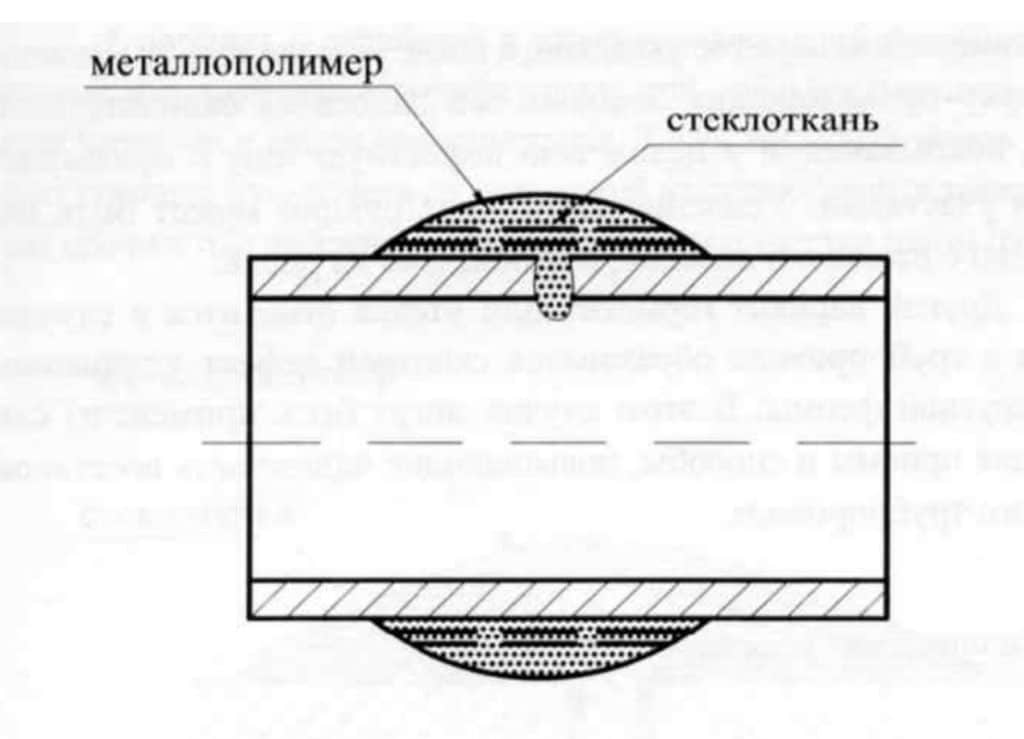
Рис. 3. Усиление места герметизации трубопровода с помощью манжеты из армирующей ленты
Усиление такой конструкции может быть выполнено с помощью металлической пластины, как показано на рис. 4.
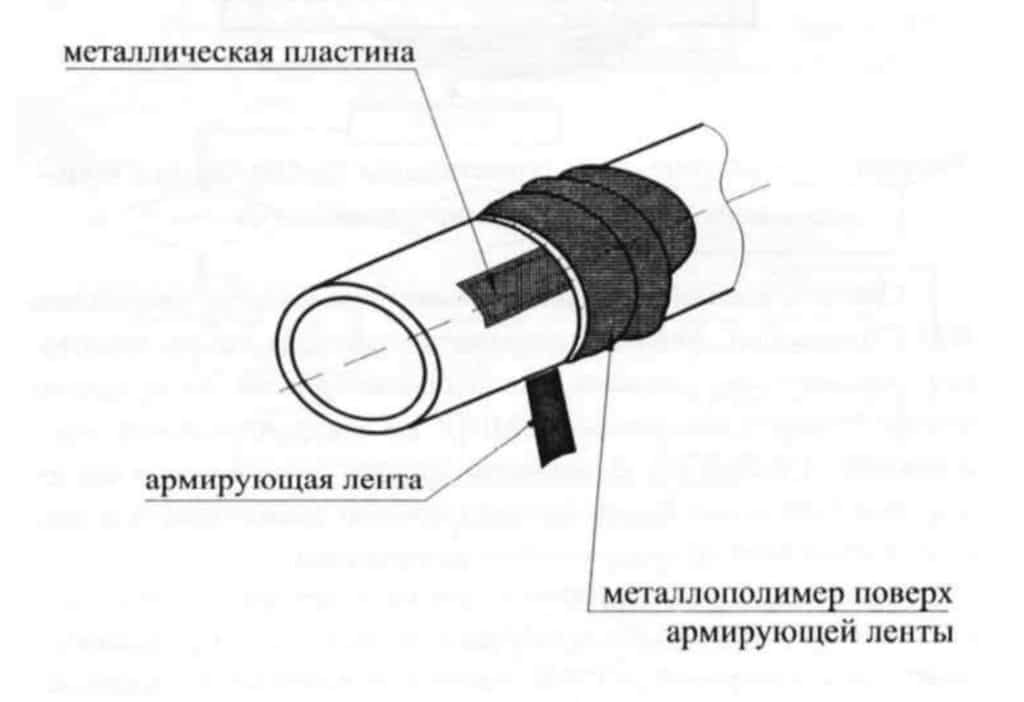
Рис. 4. Дополнительное усиление места герметизации с помощью пластины.
Другой пример герметизации утечек относится к случаю, когда в трубопроводе образовался сквозной дефект удлиненной или круглой формы. В этом случае могут быть применены следующие приемы и способы, повышающие надежность восстанавливаемого трубопровода.
Первый вариант включает в себя установку закладного элемента – пластины с двумя проволочками (рис. 5), которая вводится в отверстие и изнутри трубы прижимается к дефектному участку путем того или иного способа удержания пластины за проволочки (например, путем накручивания их на стержень, опирающийся на наружную поверхность трубы). Затем выполняется втирание МПМ н нанесение основного слоя. Такой способ значительно повышает надежность выполненной герметизации.
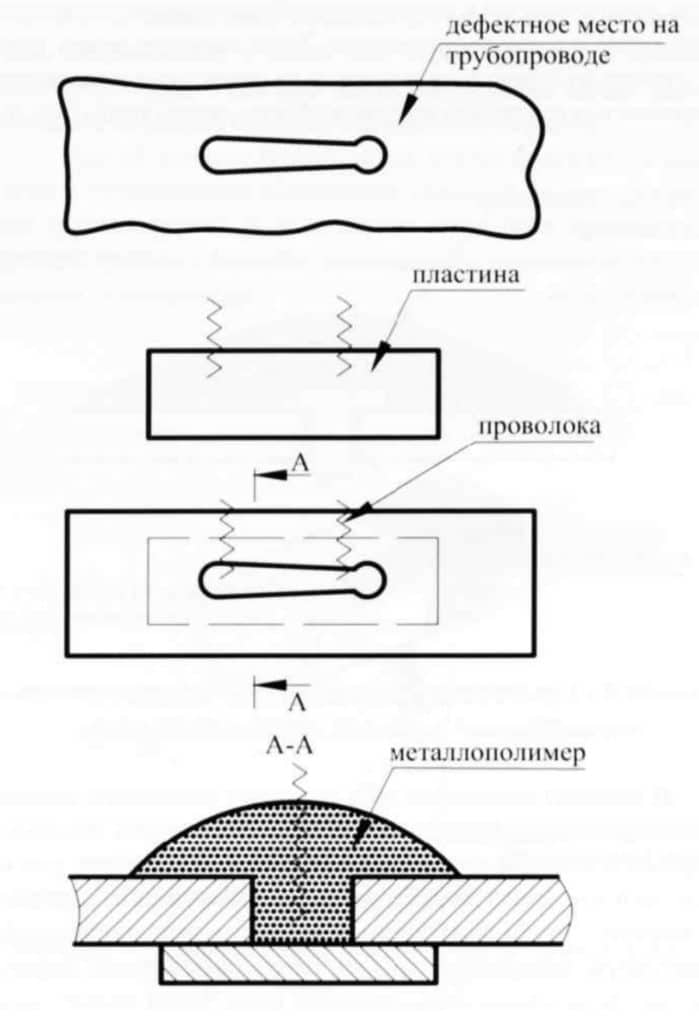
Рис. 5. Схема установки пластины и нанесения материала.
Второй вариант предполагает использование магнитных пластырей на постоянных магнитах, позволяющих удержать пластину, как показано на рис. 6, в требуемом положении, с последующей герметизацией места утечки МПМ ускоренного отверждения. Такая конструкция может создавать силу прижатия от 5000 Н до 10000 Н при собственной массе магнита 4,7 – 8,7 кг.
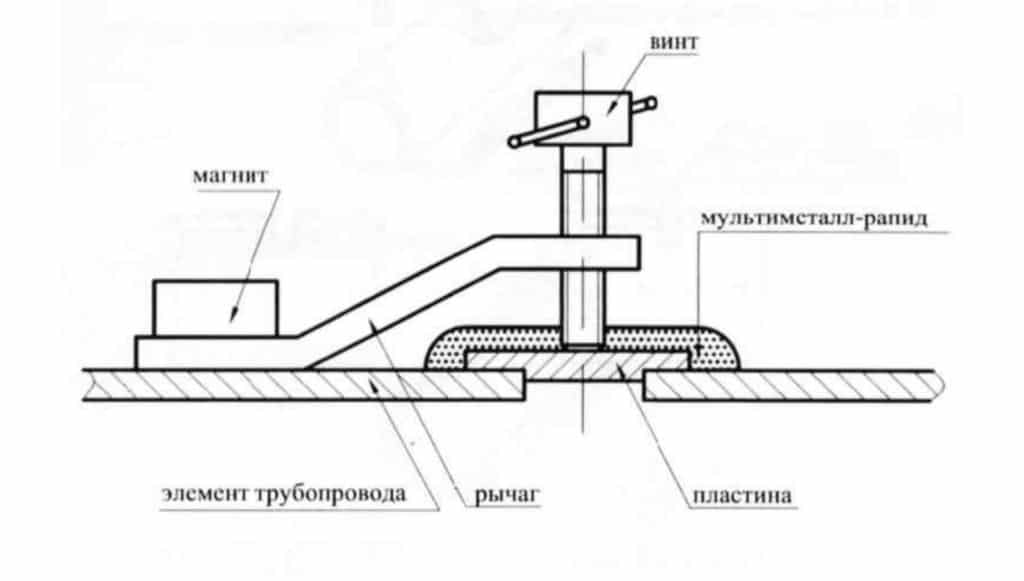
Рис. 6. Герметизация дефектного участка трубопровода с использованием магнитного пластыря.
Третий вариант требует применения дополнительной оснастки в виде мелкоячеистой металлической сетки и формирующего его инструмента. На рис. 7 показана последовательность таких операций.
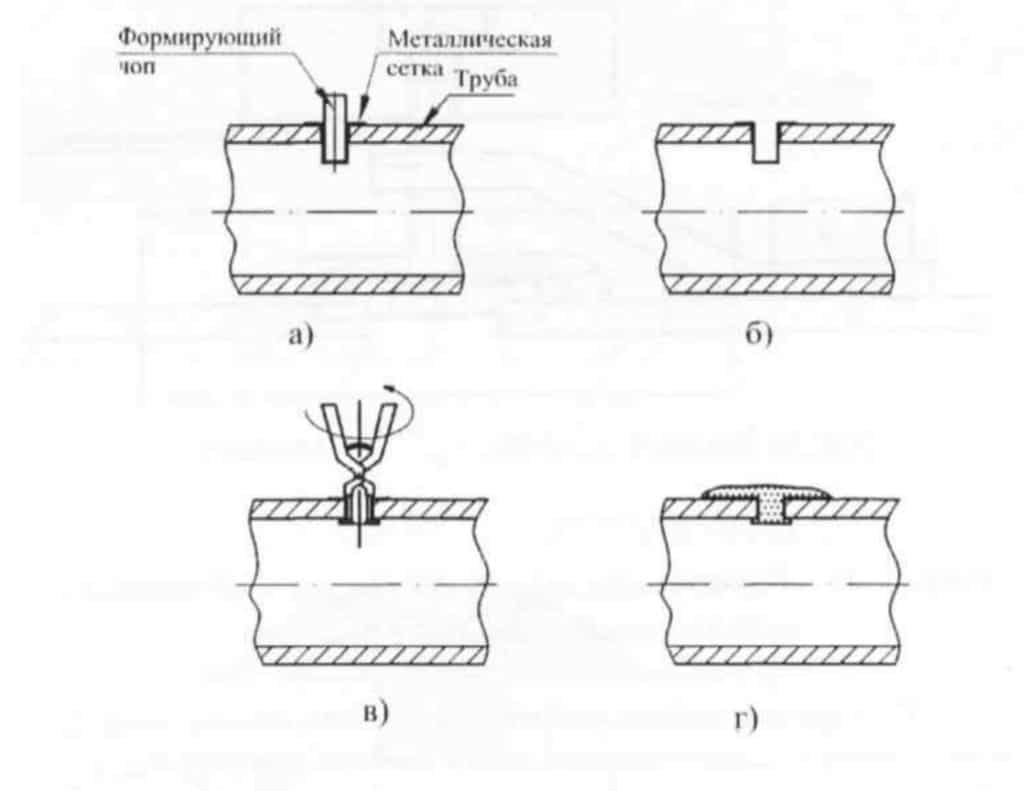
Рис. 7. Схема формирования заклепки из металлической сети и МПМ.
Вначале сетка укладывается на отверстие и деревянным чопом, равным диаметру дефекта, вдавливается вовнутрь. (рис. 7а), формируя из сетки цилиндр, опирающийся своими заплечиками на наружную поверхность трубы (рис. 7б). Поверхность, окружающая дефект, зачищается, обезжиривается, и на нее наносится слой МПМ. Затем сетка вставляется в отверстие и специальным инструментом из нее формируются заплечики уже внутри трубы (рис. 7в). После того, как инструмент извлекается из отверстия, дефектное место покрывается «мультиметаллом» (рис. 7г). Очевидно, что такой способ наиболее эффективен, поскольку не требует дополнительной оснастки и сложных инструментов и в то же время гарантирует герметичность трубопровода в любых условиях эксплуатации.
Четвертый вариант разработан центром технической диагностики «Диаскан» (Россия) и представляет собой достаточно сложную конструкцию в виде двух полумуфт, охватывающих трубу в месте дефекта, как показано на рис. 8.
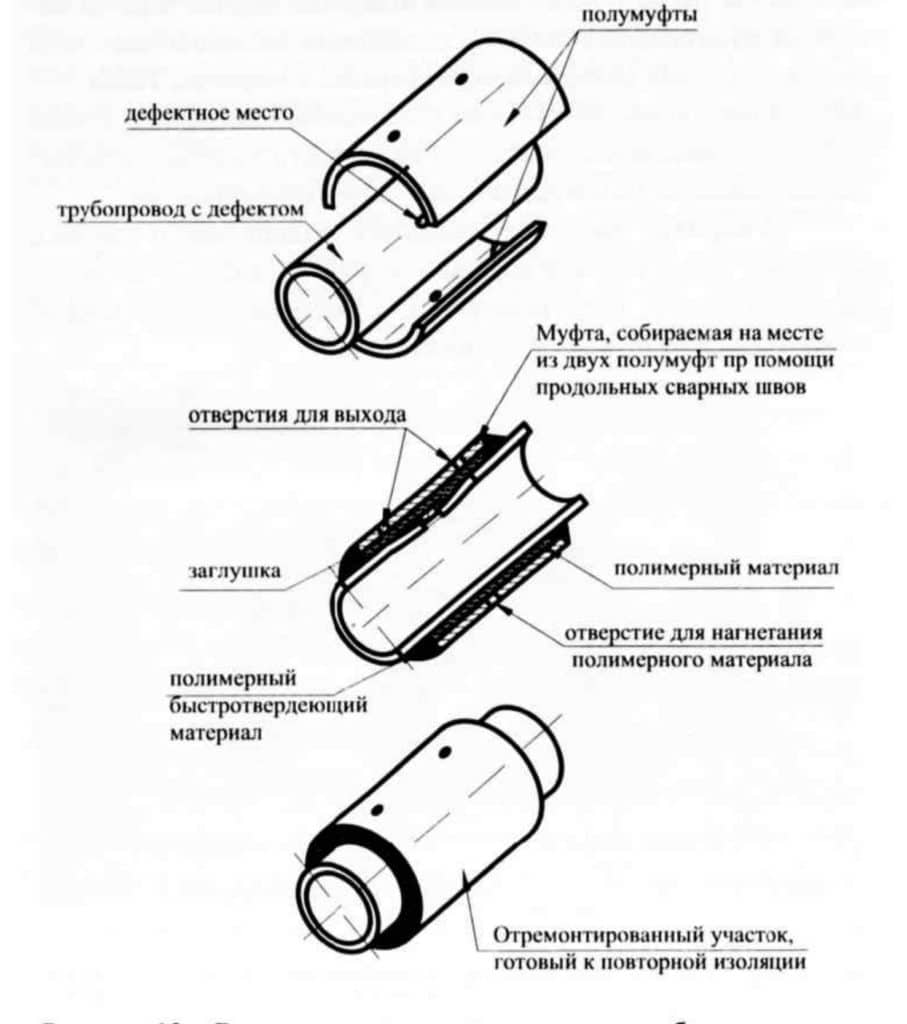
Рис. 8. Восстановление поврежденного трубопровода с помощью муфты и полимерного материала.
В отверстие вставляется заглушка, полумуфты свариваются и выставляются с помощью установочных винтов (на рис. 8 не показаны) с зазором относительно трубопровода. Затем торцы образованной конструкции герметизируются быстроотвердеющим материалом рапид и через нижнее отверстие ведется закачка материала жидкотекучий МПМ с помощью инъекционного пистолета до выхода материала через нижние отверстия. Такая технология восстановления сложна и недешева, однако, вне всяких сомнений, имеет высокую степень надежности в случаях ответственных ремонтов на магистральных газо- и нефтепроводов.
Пятый вариант предполагает установку традиционного хомута с резиновой манжетой, как показано на рис. 9, который после затягивания хомута герметизируется и усиливается с помощью стеклоткани и материала «мультиметалл».
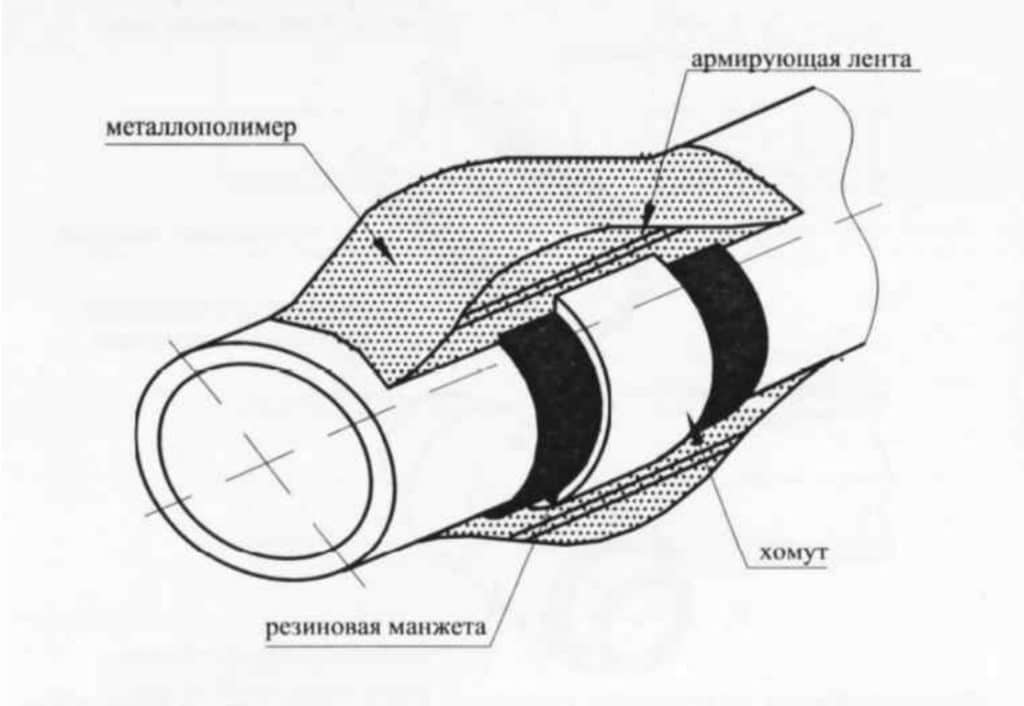
Рис. 9. Герметизация «мультиметаллом» резиновой манжеты, зафиксированной с помощью хомута.
Еще одни возможный дефект трубопроводов и емкостей – это утечка продукта по сварному шву. В этом случае МПМ наносится тонким слоем на место утечки в сварном шве после соответствующей зачистки шва, обезжиривания и просушивания. Выполнение такой работы по герметизации сварного шва бензо- или газопроводов должно сопровождаться соответствующими мерами безопасности (исключение электрических зачистных машинок и применение ручной затирки щетками с медными проволоками).
Таким образом, проведенные исследования и представленные выше технологии устранения сквозных свищей в трубопроводах с помощью полимеров, прошедшие промышленную апробацию, прежде всего на нефтепроводах России, позволяют рекомендовать эти виды ремонтов для более широкого использования в различных отраслях промышленности Украины.
Оставить заявку